现代工业制造生产中,自动点胶插磁组装机 作为一种高标准的自动化组装设备。广泛应用于电机制造、电子设备组装、汽车零部件生产等领域,尤其是在电机转子和定子的组装过程中,能够显著提升电机的生产效率和产品质量。但,尽管自动点胶插磁组装机具有一定的生产优势,许多制造企业在实际应用中仍面临诸多痛点,这些问题不仅影响了设备的性能,还制约了企业的生产效率和产品质量。
例如,某电机制造企业在采用自动点胶插磁组装机时,时常发现磁钢插装位置出现偏差,导致磁场分布不均,影响电机性能。同时,点胶过程中胶水溢出或未完全覆盖的问题也时有发生,导致产品返工率高。此外,磁钢的极性错误、设备兼容性差以及生产效率低下等问题。这些问题的产生不仅增加了生产成本,还影响了企业的市场竞争力。
针对这些问题点,本文将深入分析自动点胶插磁组装机在生产过程中存在的问题,并提出针对性的解决方案,以帮助工业制造企业提升生产水平,推动生产自动化和智能化的发展。
首先,我们先针对自动点胶插磁组装机中的生产痛点逐一进行分析。
(一)定位精度不足:在自动点胶插磁组装机生产时,定位精度乃是一关键问题。磁钢插装位置的偏差会导致磁场分布不均,影响电机的性能和效率。同时,点胶位置的不精准也会导致胶水溢出或未完全覆盖,从而影响产品电机的密封性和可靠性等。这些问题的根源可能在于设备的传动系统误差、缺乏高精度定位系统或设备老化等因素。
(二)极性错误:这一问题在制造企业生产中是一个常见但会严重影响产品质量问题的因素之一。极性错误会导致磁场相互抵消,降低电机的扭矩输出和效率。人工检测极性效率低且容易出错,而缺乏自动检测装置则进一步加剧了这一问题。
(三)设备兼容性差:不同型号的磁钢或点胶组件在设备上的兼容性问题,严重影响了生产效率。且设备升级或更换零部件时,停机时间长,无法无缝对接。这些问题的根源在于设备设计缺乏模块化、接口标准不统一或软件支持不足等。
(四)生产效率低:生产线停机时间较长、零部件配送效率低下、人工操作流程繁琐以及点胶和插磁过程的速度慢,都是导致生产效率低下的原因。在生产中自动化程度不足、配送流程不合理或设备性能不佳等,都是需要解决的关键问题。
针对上述其生产痛点,我们的解决措施如下:
1.提升定位精度:引入高精度定位系统,如视觉识别系统和激光定位技术,实时监测和调整磁钢及点胶位置,确保精度位移的准确。同时,升级传动部件,减少机械误差,提高设备整体的定位精度。
2.解决极性错误:在设备中增加自动极性检测装置,确保每一块磁钢的极性正确。然而,合利士在插磁组装过程中,通过将磁钢分别以N极与S极的标记放置在不同区域,并集成极性检测功能,能够精准无误地区分N极与S极的磁钢,有效避免了极性错误,提升后续装配的准确性和安全性。
3.提升设备兼容性:采用模块化结构,将设备的各个功能模块化,便于更换和升级部件。同时,通过软件升级,优化设备的兼容性,减少因硬件差异导致的问题。
4.提高生产效率:引入自动上料机、自动拧紧机等设备,减少人工干预等。此外,引入智能化仓储管理系统,实现零部件的快速配送和精准管理。
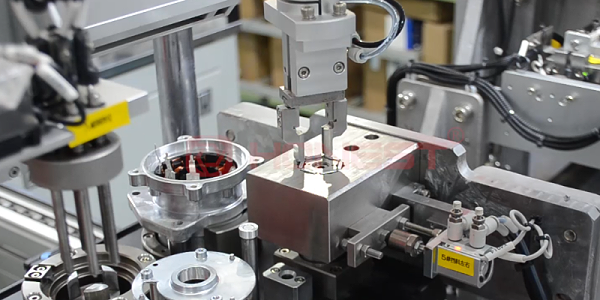
对于电机制造企业而言,自动点胶插磁组装机是现代工业制造生产的重要设备,其性能直接影响生产效率和产品质量。通过以上的关键解决措施,制造企业不仅能有效解决自动点胶插磁组装机的技术难题,还能显著提升生产效率和产品质量,降低返工率和生产成本。更重要的是,这些解决方案为电机制造企业的自动化和智能化转型奠定了基础,推动装配工艺迈向高效化、智能化的新阶段。